Our News
Not to miss
QUALITY AND PERFORMANCE AT THE HEART OF OUR CONCERNS !
Quality and performance are at the heart of our concerns in order to bring total satisfaction to our customers.
The quality, continuous improvement, production and technical teams are being trained on the theme of zero defects, integrating quality into their daily work.
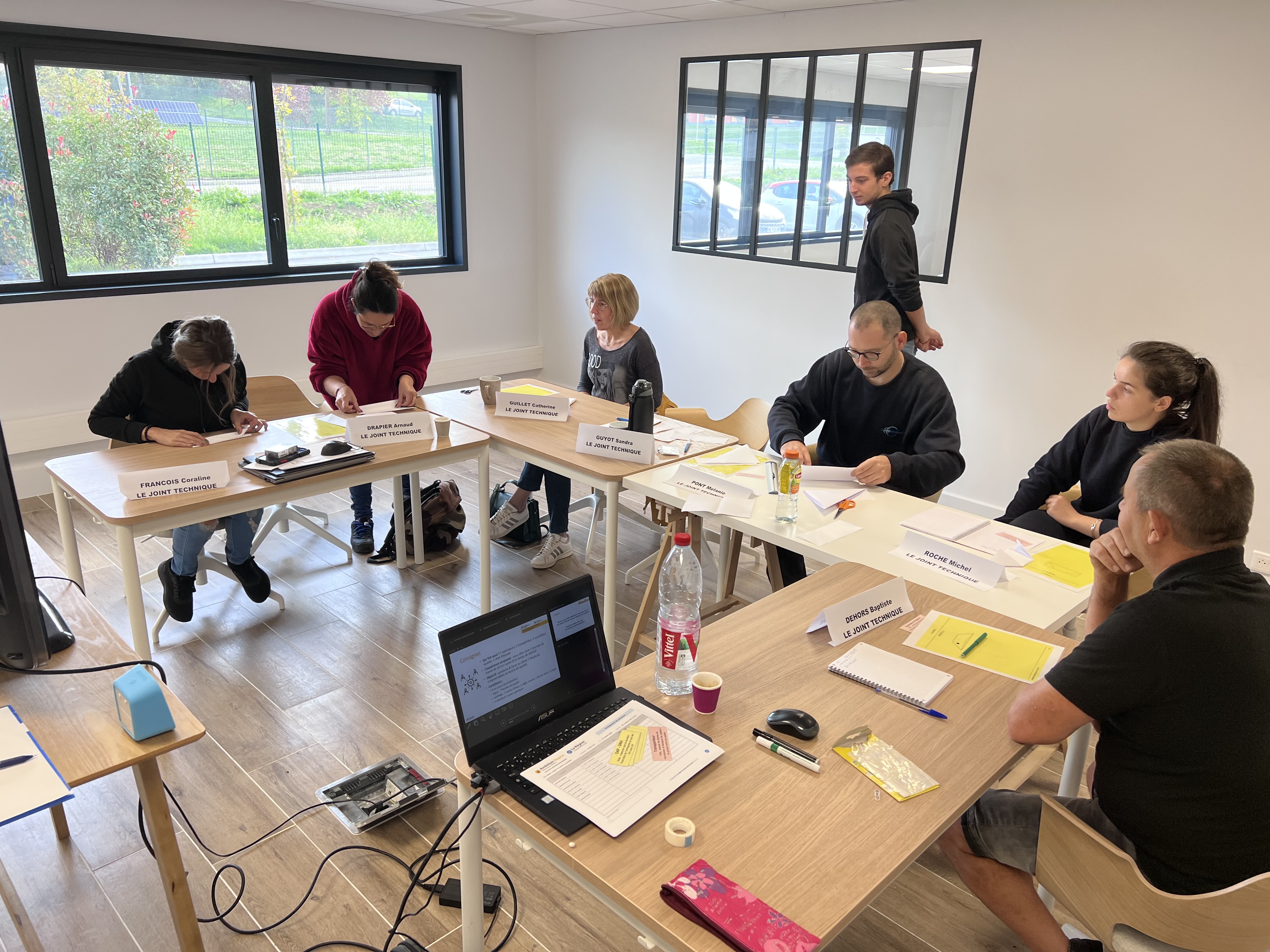
Kaizen Week
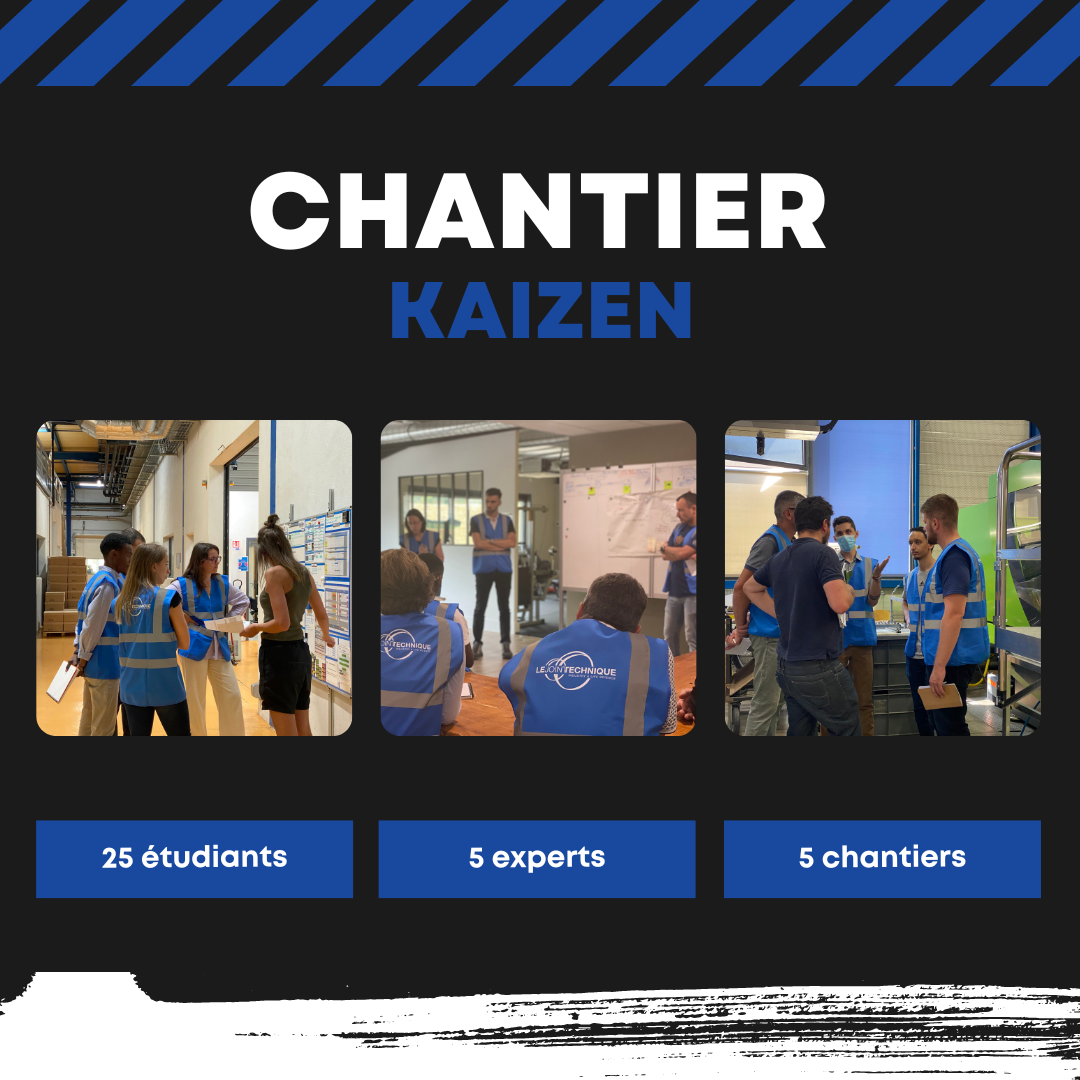
10 years later, we had the opportunity to repeat the Kaizen Week experience !
This method advocates continuous, progressive improvement at all levels of the company.
The objective is to improve the company's productivity while valuing individuals at their workstations and using existing resources.
This kind of event shows the strength of the group and the cohesion it can generate.
The ECAM students were able to come to our premises and deal with 5 improvement projects:
- Project 1: Reduce the processing time for new products in project mode in our cutting activity and make operations more fluid until the production launch.
- Project 2: Reduce our customer delivery times in our cutting activity.
- Project 3: Reduce the non-quality in the Injection activity and improve the management of defective parts.
- Project 4: Increase the number of parcels shipped per day from 10 to 100 for our lace startup GORILLA.
- Project 5: Optimise flows between the two sites and manage space.
We wish to take advantage of this dynamic to deploy a permanent improvement approach in the company.
We are pleased to present our new factory.
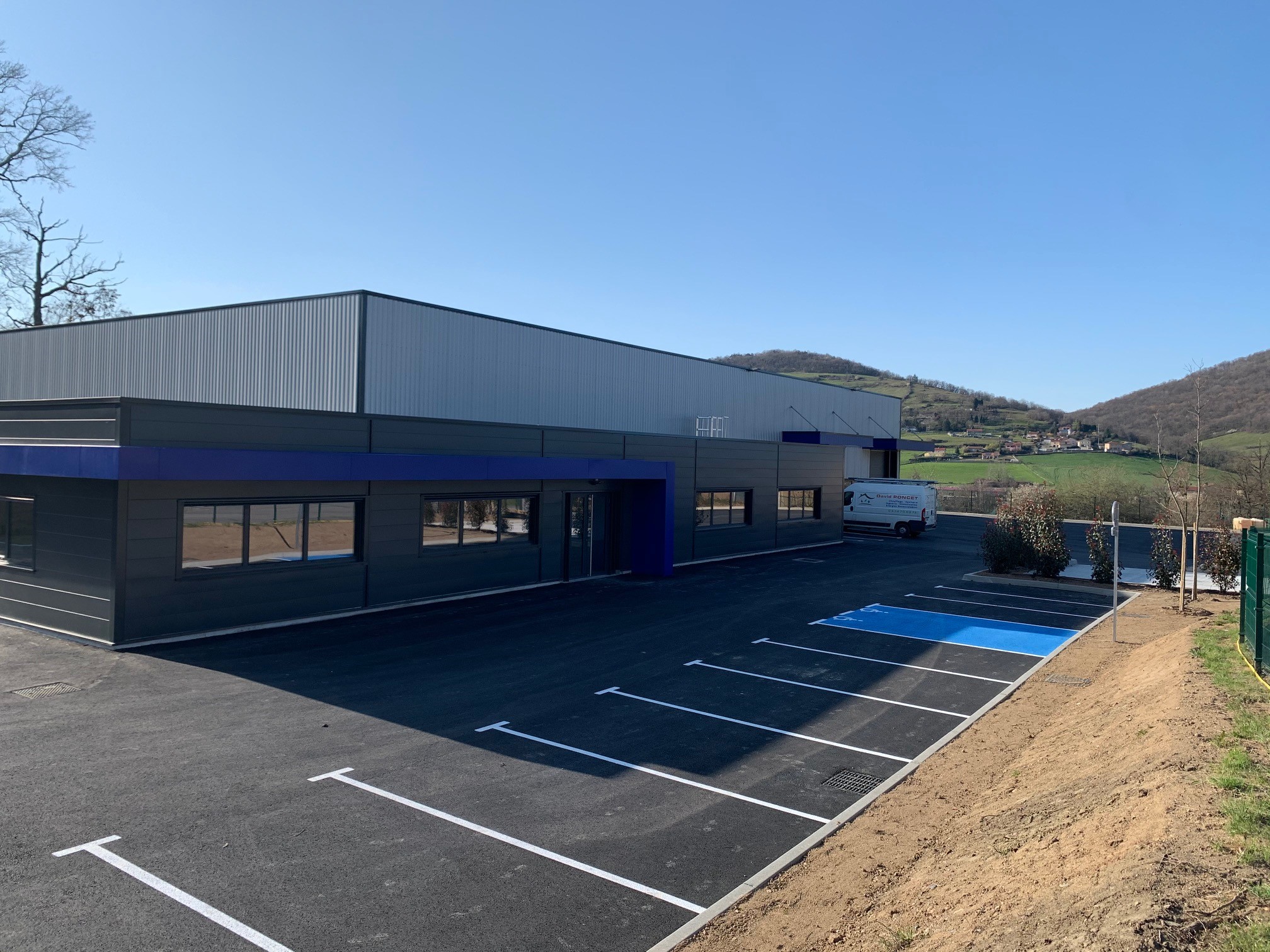
It is with great joy that we can finally confirm that our new building is ready and operational !
With a surface area of 2,500 m² and located only 70 metres from the existing building, it will support our development project and allow us to :
- Double our surface area for silicone injection
- Create a new ISO 5 clean room for our medical and pharmaceutical activities
- Consolidate our silicone HARDCOAT activities in a new production unit in an ISO 7 environment
- Double the surface area of our cutting workshop
- Create a tooling maintenance workshop
- Grouping together our vision camera machines in a quality centre.
Our storage area, now separate from production, is secure and better adapted to our flows.
As for our autonomous production units, they are now optimised for the development of our product/process and market expertise in order to better meet our customers' expectations.
We wish you...

Thank you so much for the year that has just passsed !
We hope to have contributed to the success of your projects.
Now and tomorrow, let us seize the opportunities and new challenges together and have our daring and passion open up new horizons !
Happy Season's Greetings !
Happy New Year 2020 !
your project has an appointment with our expertise

LE JOINT TECHNIQUE will participate in the MIDEST 2019
We will meet you from March 5 to 8 to discuss your sealing issues and solutions that we can offer.
STAND 6K167
Rapid prototyping
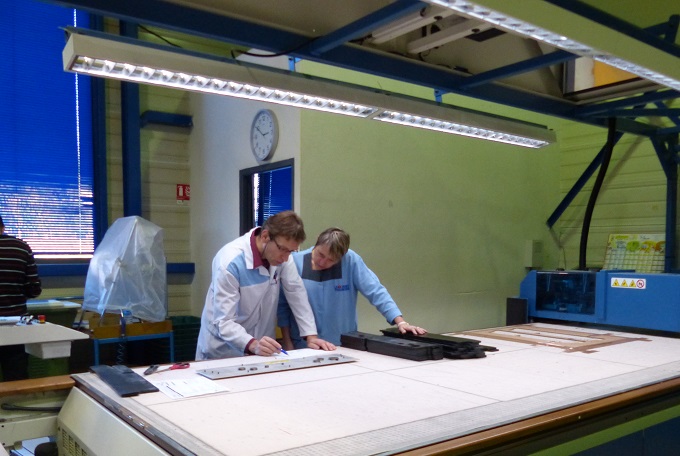
The possibilities offered by the current 3D design tools have led to an impressive speed-up of the development phases.
Nevertheless, new functions or new concepts, etc. occasionally need to be validated... but there is not enough time for this!
This is where rapid prototyping comes in. Solutions for plastic and metal have been available for a long time now: powder sintering,stereo-lithography, machining, etc.
For flexible materials, the solutions were more limited.
LJT can now offer a range of solutions in order to obtain representative parts within a few days:
- digital cutting for flat seals made from foam, elastomers, composites or others
- 3D printing for formed parts made from silicone, regardless of their hardness or color
- machining of rotationally-symmetrical parts made from elastomers or plastics (POM. PA, PTFE).
Generally speaking, machined elastomers are limited to high hardnesses (85-90 shore A).
LJT differs in that it has a more standard range of hardnesses (70 shore A), or even lower (40/50/60 shore A).In any event, there is no need to develop a tool; a 2D or 3D file of the part will suffice.
Don't hesitate to contact us!
Our production site in Tunisia
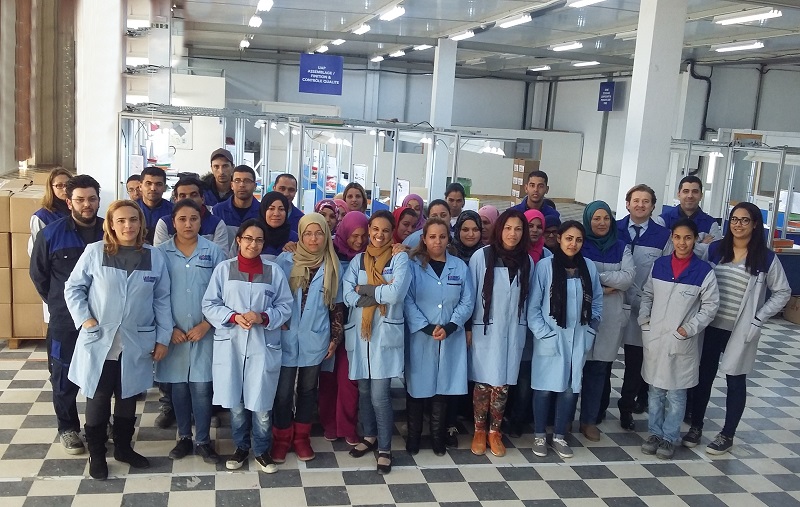
LJT was established in 2006 in Tunisia, mainly to support our European markets and customers.
The site is located in Gammarth, which is to the north of Tunis and just 15 minutes from the airport.The site is certified ISO 9001: 2015 and IATF 16949: 2016.
It operates in line with the group’s standards: projects are managed in France and then transferred to Tunisia.
The site extends over an area of 2700 m², is split into three production units for 50 people and boasts a modern, powerful fleet of machines thanks to a sustained investment policy.
- injection of molded parts and O-rings made from rubber, rubber silicone, thermoplastic and liquid silicone
- cutting of delicate materials (rubbers, foam, composites, cork, paper, etc.)
- assembly to offer you a comprehensive solution
To increase the synergies and secure the transfers, the site is now equipped with metrology in the form of an automatic optical 3D measuring machine, identical to the one used on our site in France.
Our respective laboratories are now equipped with the same capacities and the same resources.
HARDCOAT coating: expertise and ambitions
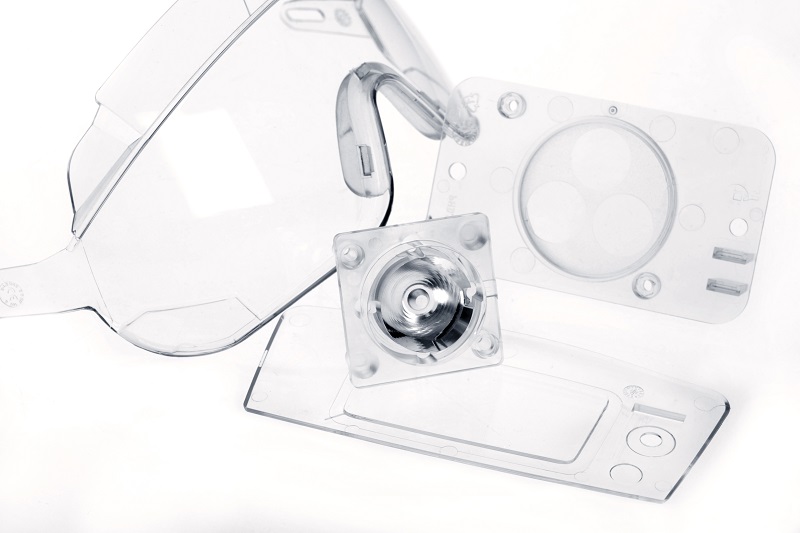
To meet demand on the French market, LJT integrated this technology in 2000 in partnership with a silicone HARDCOAT varnish manufacturer.
We are now establishing ourselves as a key player in France in this HARDCOAT coating activity.
The aim of a HARDCOAT coating is to protect polycarbonate and PMMA – which by their very nature are fragile – against abrasion, adverse weather, chemicals, UV and yellowing, etc.
We work in a clean room to guarantee an optical quality and to control the particles on visible parts.
It has multiple applications; we are involved in all markets, particularly aeronautics, rail, lighting and optical, medical and automotive, etc.
In order to respond to new requirements and higher demand, an investment program will soon be launched. This will enable us to expand and handle our capacities (dimensions and design) for quantities of between one and several hundreds of thousands.
Flashless, a flawless technology
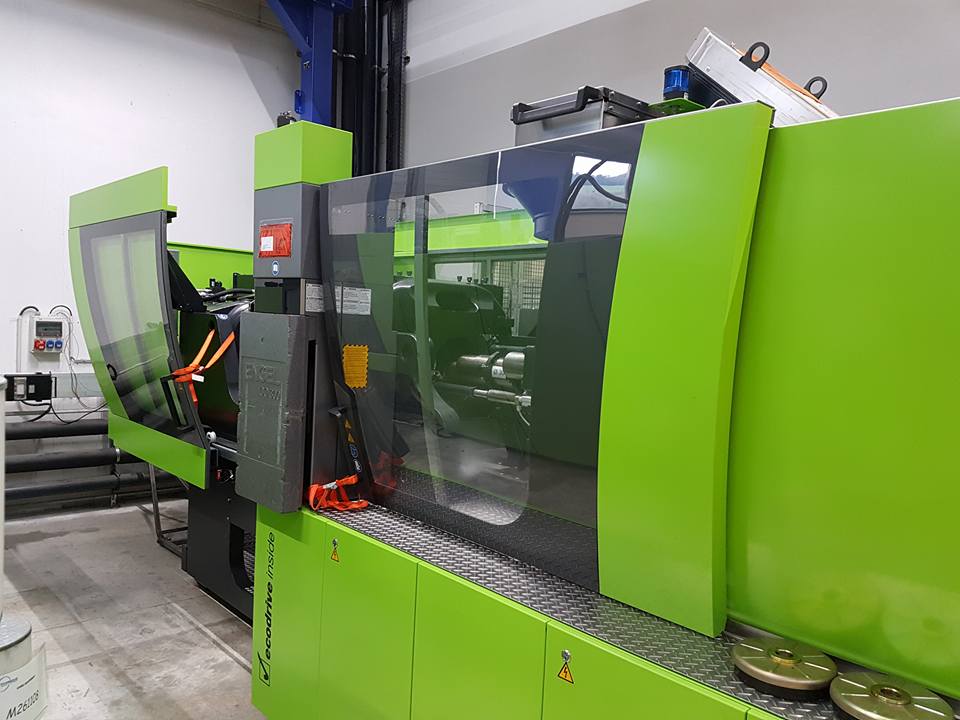
Typically, and by analogy with the existing situation, the transformation of rubbers and rubber silicones takes place in layers.
The flash generated by the complete filling of the impressions is then refinished, either by means of cryogenics, tribofinishing or manual deflashing.
LJT now has a modern, attractive alternative: flashless technology.
This flashless molding technology has many advantages:
- Material gain of approximately 15 to 30%
- Finished parts at the foot of the press
- Automation, robotization
- Gains on annual capacities
- Cleanliness of finished parts
This technology is justified for the production of large series because the investments in tools and robotization are significantly higher than for a traditional equipment.
INTERVIEW WITH A COLLEAGUE

Our colleagues talk about their job.
We pursue our series of articles in which we meet the men and women who contribute to the rich tapestry of our company.
Today, let’s meet Céline GOUNON| QSE Manager – Lean Manager|
- Céline, tell us about yourself ? What is your professional background?
QSE Manager – Lean Manager at LJT. I joined the LJT team in October 2013. I used to work in a large heavy metallurgy organization, and my initial training was in QSE. I returned to studying in 2012, at ECAM School of Engineering, where I was awarded a Post-Masters (bac + 6) degree in “Lean Management and Continuous Improvement".
- What exactly is the role of QSE Manager – Lean Manager?
Ensuring that our internal and external customers are satisfied while offering an appropriate level of quality. Our markets– and therefore our customers – do not have the same requirement levels. “Over-quality” is just as much of a disadvantage as “non-quality”. As a Lean Manager my role is, above all, that of a coach, to enable the teams to flourish in terms of their autonomy in a comfortable and effective working environment.
- Which are your favorite aspects of your job?
Relations with others. I have a cross-functional role that allows me to work with all interested parties : internal players (management, operators, support services, Tunisian site),and external players : customers and suppliers as well as other bodies such as healthcare and safety services (e.g. occupational medicine, local authorities).
- Can you describe your working day in 3 points?
The operating standard for production has very recently become 3x8.
1- When I arrive, I work my way around the company’s various departments to greet the teams and to find out if everything is going well. I do the same thing for the teams in the afternoon.
2- I lead the production meeting (UAP) at 9 am every morning. After these two rituals, my schedule for the day is finalized.
3- In the mornings I tend to focus on work in the field, and in the afternoons I tend to work more on formalizing standards, resolving problems, indicators and miscellaneous customer documentation.
- Which project(s) have you particularly enjoyed working on?
All projects at Joint Technique are exhilarating, but one of the most memorable was the “cutting/machining” one.
This project took a year for the industrialization phase. For me, it was a huge playground where I was able to set up the Kanban, define the operating and quality standards, train the teams and, above all, work very closely with the customer in a win/win partnership.
This project is currently a pilot project for the rest of the company.One of my ongoing tasks for this year is to improve the performance of the UAPs with complete autonomy and well-being in the work.
This sort of project can reveal previously hidden skills amongst our colleagues.
- What training would you like to do next? And which conference/professional event would you like to attend next?
“Elence” is a regional program that places humans at the heart of the company’s global performance by working on health, safety and motivation issues. This is a brand new program that is dear to our heart because it will enable us and all of our teams to grow..
LJT is one of the pilot companies in this respect.
- Do you like working at LJT? And can you tell us why?
I find the work at LJT really enjoyable: There is trust at every single level. Team spirit and people’s willingness to listen are rare assets that are firmly entrenched in our company culture. This means we can do great things and rise to challenges that few other companies can do so flexibly.
What has allowed me to flourish is the support and the increase in the teams' skills in terms of QSE and our continuous improvement.
My satisfaction is linked to the company’s performance (quality level, customer service rates and results of colleagues’ individual interviews).
LJT : holds IATF 16949 et ISO 9001:2015
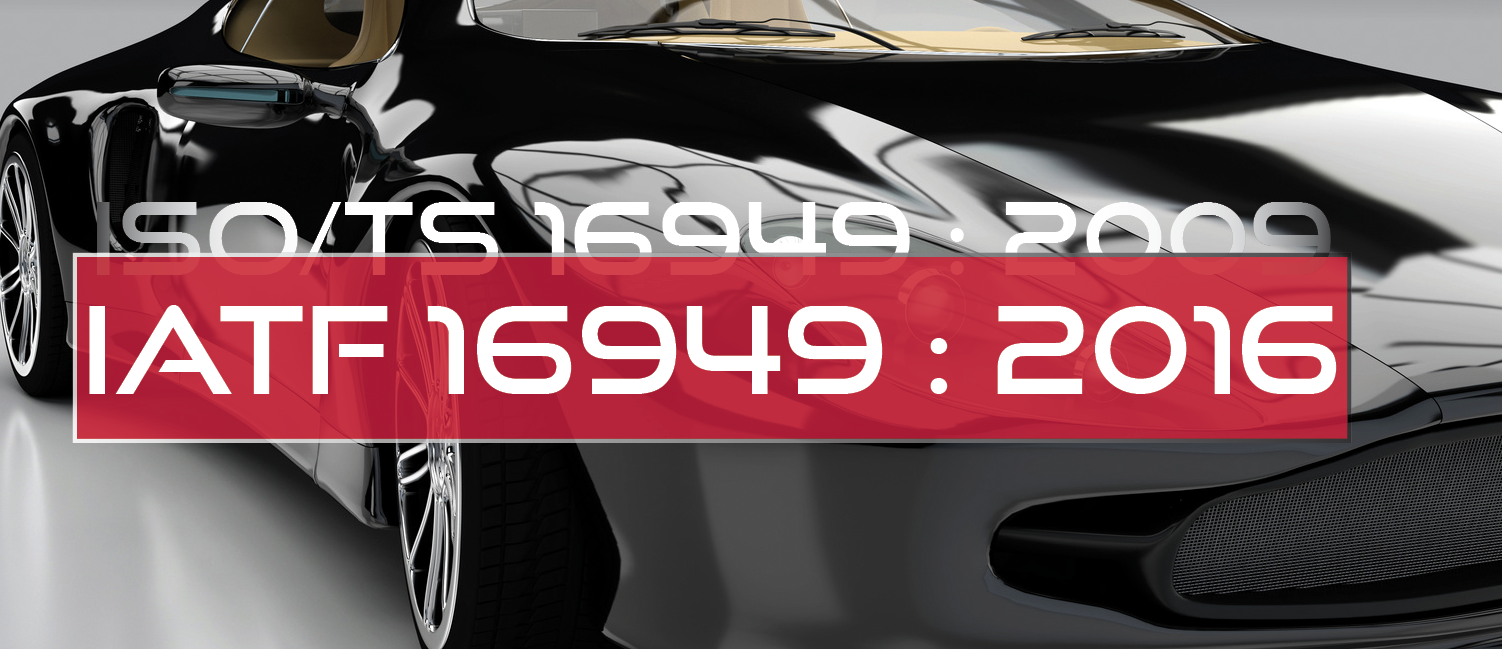
Notre vocation est de développer et réaliser des pièces d'étanchéité dans le respect de vos exigences réglementaires et légales.
Pour vous, nous avons franchit une nouvelle étape avec l'obtention de la certification IATF 16949 !
Cela nous permet de confirmer notre système de management en termes d'amélioration continue, d'analyse et de prévention des risques, de la satisfaction clients et de nos parties interessées.
LE JOINT TECHNIQUE is pleased to announce its presence at the MIDEST show in Paris Villepinte, from March 27th to 30th, 2018
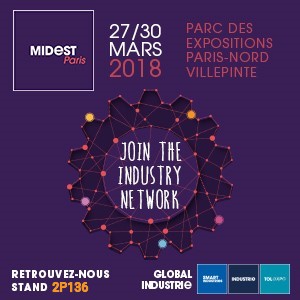
If you wish to organize a meeting with one of our staff on site, we invite you to contact us now!
By mail: contact@lejointtechnique.com
By phone: 04 74 26 32 69
See you soon on our stand (2P136) !
New projects ... New technologies
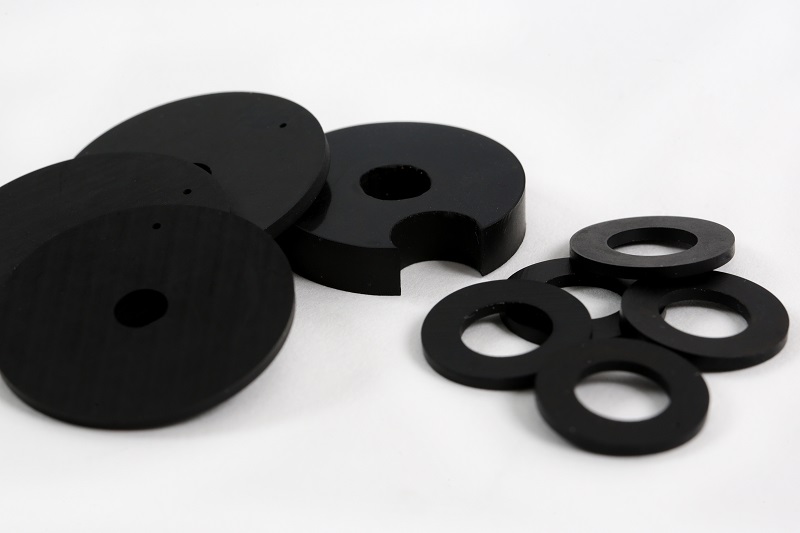
LE JOINT TECHNIQUE was approached by a major manufacturer of high-security pressure regulators and valves which was looking for an economic industrial solution for manufacturing a broad range of high-precision membranes and valves using diverse and varied materials: EPDM, NBR, FPM, Polyurethane, etc.
There was a major problem in that its requirements were not compatible with the cutting techniques available on the market:
- Tolerances of +/-0.05 for thicknesses, whereas this involves elastomers
- Tolerances of +/-0.1 for diameters of up to 40 mm and +/-0.15 above that
- Holes/vents: up to Ø0.6 mm with a depth of 1.5 mm
- Machined grooves.
LE JOINT TECHNIQUE decided to take on this major challenge!
From a blank sheet, by relying on the knowledge and experience of our design office, we came up with the SOLUTION:
- Tailoring machines and processes
- Dedicating a specific workshop
- Designing special tools
- Experimenting, testing, adapting
- New experimenting, testing, validating.
In less than two years, this resulted in LE JOINT TECHNIQUE successfully delivering some 150 miscellaneous and varied valve and membrane products, amounting to over 3 million quality parts.
This “made in LJT” technology is now attracting other sectors such as watchmaking and aeronautics.
Why not you?
First silicone 3D printing solutions
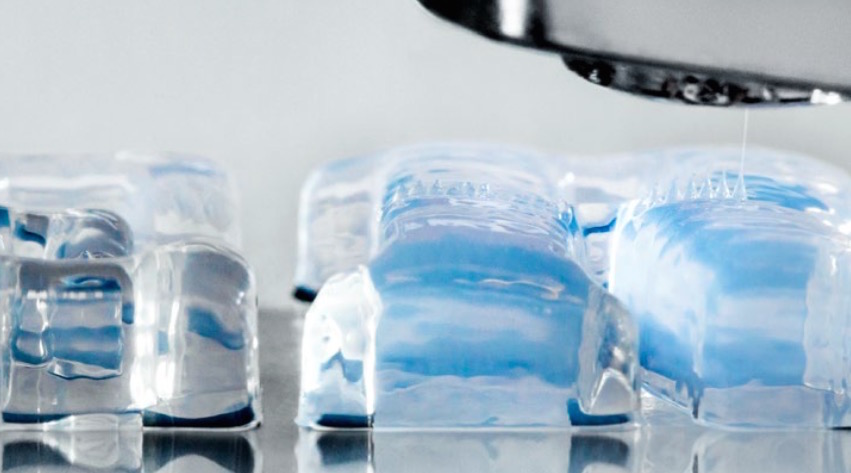
3D printing is a technology that is still new and evolving.
Not all that long ago, 3D printing was limited to metals (Metal Fusion or Additive Layer Manufacturing (ALM) and thermoplastics (Fused Deposition Modeling (FDM).
Back then, the only solution for flexible materials available to us was a polyurethane FDM – with polyurethane belonging to the large family of thermoplastics – but there was nothing for vulcanized elastomers.
The drawback of polyurethane is that it has very limited mechanical and thermal characteristics (low elastic recovery, poor temperature behavior and low compression set).
But now, thanks to the support of its Liquid Silicone Rubber (LSR) suppliers and the latest developments in these materials, LE JOINT TECHNIQUE can offer you a new silicone 3D printing technology: Drop on Demand.
This is a solution for rapid prototyping or very small series of silicone parts.It produces parts that are very realistic, both geometrically and mechanically; only the external appearance of the part differs, since graining or polishing is, of course, not possible.
With silicone 3D printing, the mechanical characteristics are almost identical to those of a molded part made from LSR. The temperature behavior is very similar to that of conventional silicones (>200°C).
This technology is already offered in several hardnesses, and even color can be added! :
- 20 Shore A : skin (Pantone 7513C), RAL 9011 Graphite Black, RAL 3000 Flame Red, RAL 9010 Pure White, RAL 5010 Gentian blue and RAL 7001 Silver Gray
- 30 Shore A, 40 Shore A and 60 shore A : Translucent, RAL 5010 Gentian blue, skin (Pantone 7513C), RAL 9011 Graphite Black, RAL 3000 Flame Red, RAL 9010 Pure White and RAL 7001 Silver Gray
It will soon become an indispensable milestone for your developments because silicone 3D printing enables you to confirm the ease of assembly and functionality of your parts very quickly and at a lower cost.
Investments made in 2018 ... 12% of the turnover
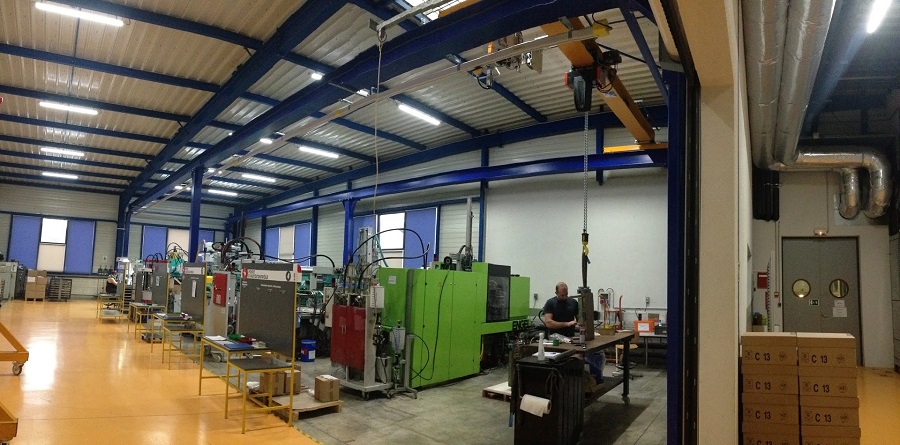
LE JOINT TECHNIQUE is pursuing a sustained investment program to support its growth policy and to maintain its high levels of service to its customers and competitiveness at an international level:
- Automation
- new technologies
- ergonomics
- 100% visual control
- digitalization
are an integral part of our investments in 2018.
This year has begun with our fully robotized liquid silicone injection workshop having just acquired a bridge crane, a new, high-capacity, connected precision oven and a press and robot unit in order to be able to start an innovative new project in partnership with a customer.
Questions for
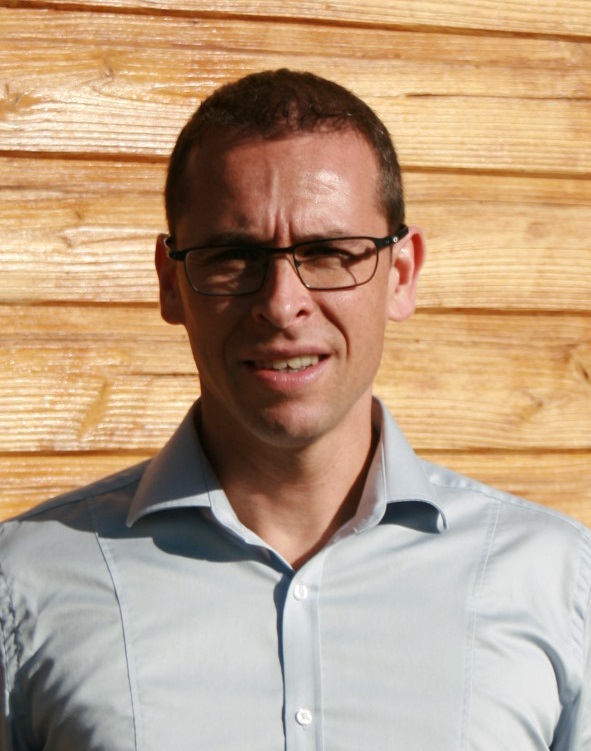
Our colleagues talk about their job... We are launching a new series of articles in which we will meet the men and women who contribute to the rich tapestry of our company.
Today, let’s meet Bruno Turpin | Industrial Manager, R&D |
- Bruno, tell us about yourself. What is your professional background?
I’m a link in the human chain that adds value to the company I work for. I’m tough on myself. I like progress because I think I owe it to others in recognition of everything they bring me. My background in a scientific sector (materials and elastomers) has allowed me to develop my skills at an international level and has, furthermore, given me an insight into other cultures.This is why I draw on the richness of human interaction for my personal and professional development.
- What exactly is the role of Industrial Manager, R&D?
The core tasks assigned to me fall into two categories:Ensuring that the company’s developments comply with requirements, technical changes and the need for profitability.Steering industrial performance thanks to the people in the organization.
- Which are your favorite aspects of your job?
Without doubt, that would be the challenges posed by the new projects and developments. We currently devise processes based on industrial agility. Each new project enables us to consolidate our knowledge, yet also to extend our boundaries.
- Can you give me three words to describe your working day?
My working day is lively and punctuated by team discussions about:
- Measurements: N-1 performance indicators review
- Analysis: Internal/external technical support
- Decisions: Actions on initiated jobs to bring about improvements.
- Which project(s) did you particularly enjoy working on?
They all have their specific characteristics and there is always a high degree of attachment to them, but I think this would have to be a project about an automotive thermal application we are currently finishing off which has involved us making some daring choices with a highly advanced and specific technology.
- What training would you like to do next? And which conference/professional event would you like to attend next?
I’ve already embarked on some training, about the factory of the future, because it’s a question of the approach needed to develop collective intelligence in our future assignments. K (the world’s no. 1 trade fair for plastics and rubber) remains one of the industry’s high points for me. I’m always looking forward to it with great excitement. The only slight downside is that it doesn’t take place in our beautiful France!
- Do you like working at LJT? Why?
I like what I do because I thrive on working in a family-owned company that gives me the space I need to fully express myself. I firmly believe that the company is forging ahead and that its ambitions are legitimate. The best proof of this is that when I look back at what we've done, I feel like saying "wow"!”
FDCA meeting
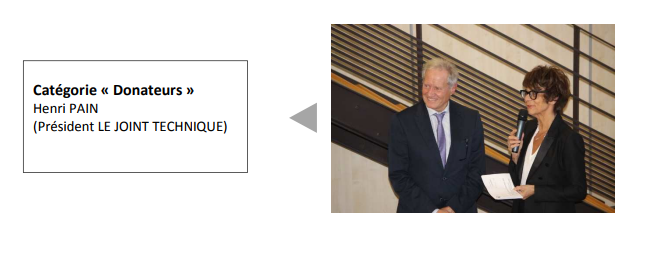
Le 8 novembre dernier, parmi les acteurs nationaux et internationaux du caoutchouc, LE JOINT TECHNIQUE a été récompensé aux rencontres de la FDCA, par l'intermédiaire de son Président, Monsieur Henri PAIN.LE JOINT TECHNIQUE, qui intègre l'innovation dans son management au quotidien et cherche à dévolopper en permanence la R&D par le biais de la veille technologique et de la formation, soutient la Fondation du Caoutchouc (FDCA).Cette dernière a pour objectif de mettre en place une structure de recueil de fonds destinés à soutenir financièrement des actions de recherche et de formation.Elle fait partie des cinq destinés à accompagner le développement de la filière caoutchouc en France et en Europe du Centre français du caoutchouc et des polymères (CFCP).
Fermeture estivale 2017
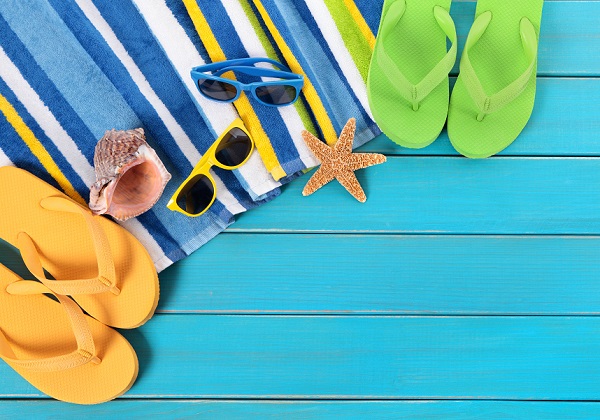
Nous vous informons que nous serons fermés du 1er au 18 août inclus. Une permanence commerciale sera assurée jusqu'au 4 août.Pensez à anticiper vos commandes pour les livraisons sur juillet et à partir du 20 août.Toute l'équipe commerciale reste à votre disposition pour planifier avec vous vos besoins sur cette période!Bonne vacances!
LE JOINT TECHNIQUE s'équipe d'une nouvelle étuve de laboratoire

La tenue en température associée au vieillissement de nos produits, est l'une des problématiques majeures dans les domaines Industriel et Automobile.C'est pourquoi, dans sa recherche permanente d'amélioration et de collaboration avec ses clients, LE JOINT TECHNIQUE investi aujourd'hui dans un nouvel outil.Cette étuve va permettre de tester et de valider la résistance aux fortes températures des joints d'étanchéité grâce à la programmation et l'enregistrement permanent des cycles thermiques.