Silicone liquide VS Silicone malaxable
Silicone liquide
Le silicone liquide (LSR) regroupe toujours à minima deux composants (A et B) tous deux liquides. Ces matières demandent des périphériques d’alimentation spécifiques pour acheminer les composants, et les mélanger.
Ils présentent une très faible viscosité qui facilite la transformation en moulage par injection, et permet aisément de travailler avec un grand nombre d’empreintes dans les outillages (moules). Cette propriété offre l’avantage de permettre une technologie sans bavure (flashless), la pièce sort ainsi finie du procédé d’injection. En outre, les silicones liquides offrent une transparence autorisant un panel de couleur presque sans limite.
Les limites d’utilisation des LSR se situent sur des applications très basses températures (<-55°C), ou sur des applications avec des exigences de résistance en déchirement élevées, ou alors dans des applications qui requièrent des propriétés d’amortissement dynamique. Enfin, la performance du système de catalyse, qui autorise des temps de cycles très intéressants, rendent également le produit plus onéreux.
Silicone malaxable
Le silicone malaxable se présente sous forme d’une matière solide et compacte, généralement prête à l’emploi, elle intègre des constituants similaires (même famille) à ceux employés dans les silicones liquides. Sa viscosité très différente permet une manipulation plus directe sans besoin de périphérique, mais rend plus difficile et plus consommateur d’énergie l’acheminement, et le remplissage des empreintes.
En conséquence, la maitrise de la bavure est plus complexe, et des opérations de finitions en ébavurages sont parfois nécessaires. L’amplitude des propriétés mécaniques de la matière permettent d’assumer des fonctions d’amortissement, le silicone malaxable peut s’avérer un choix intéressant là où les silicones liquides affichent quelques limites thermo-mécaniques.
En revanche, les possibilités de colorations ne sont pas aussi larges que pour la gamme des silicones liquides, mais les coûts unitaires au Kg sont généralement bien plus avantageux. Enfin, grâce à une viscosité favorable, cette gamme offre la possibilité d’une transformation par extrusion, et donc la réalisation directe de profilés.
Conclusion
Le silicone liquide fait appel à une technologie de transformation plus complexe et plus chère, mais permet des niveaux de productivité intéressants dans l’utilisation des grades standards.
Le silicone malaxable quant à lui reste une alternative de choix, là où les besoins fonctionnels exigent des performances spécifiques nécessitant des formulations dédiées aux applications.
Vous l’aurez donc compris, le choix du type de silicone dépend surtout de vos besoins !
N’hésitez pas à nous contacter, nous pourrions vous aider dans vos projets de conception.
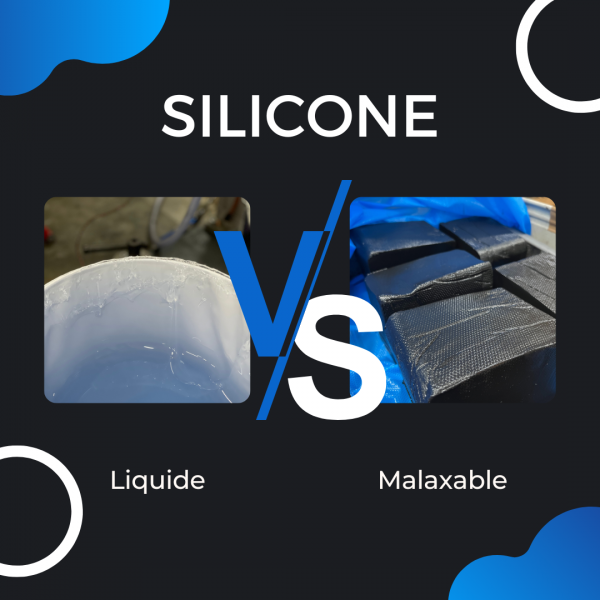